品質管理とは?品質保証との違いや実践で役立つ9つの手法をくわしく解説
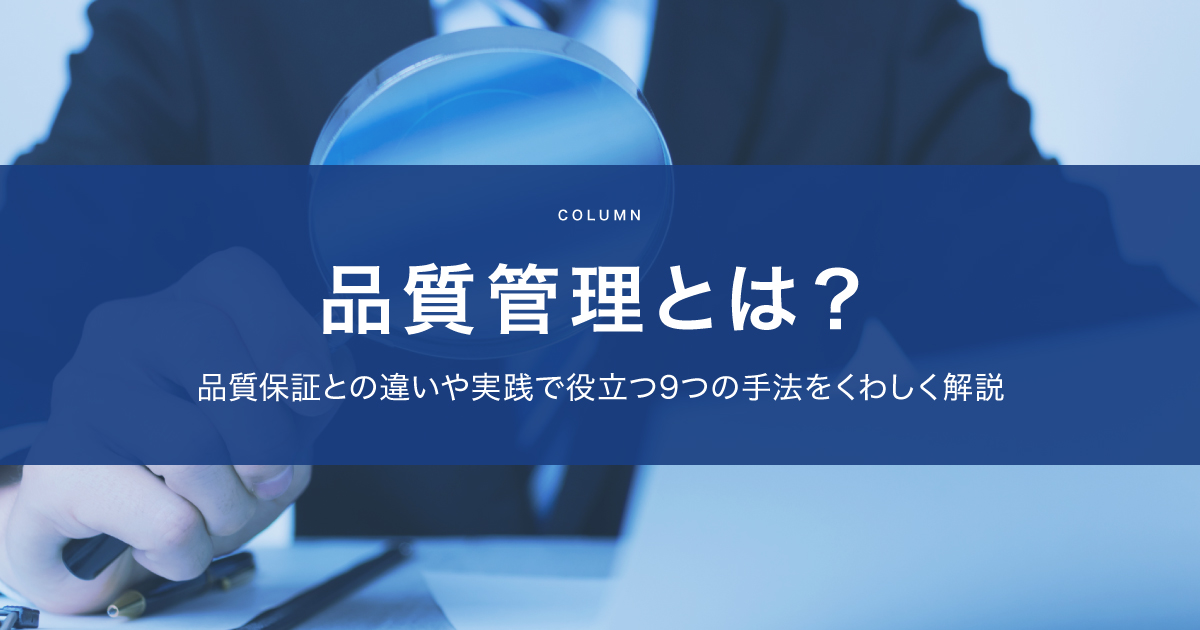
製造業における品質管理とは、製品を生産するにあたって、品質向上と一定の品質を備えるために、検査、検証し、保証することです。製造業において重要なQuality(品質)・Cost(コスト)・Delivery(納期)を最適化し、顧客の信頼と満足を得るための仕事には必須と言えます。この記事では、品質管理に必要な3要素や使われる9つの品質管理手法、おすすめのシステムなどについてご紹介します。
品質管理とは?
製造する製品において品質の一貫性を確保するために欠かせないのが品質管理です。品質管理業務の基本とその重要性について、みていきましょう。
品質管理の基本。なぜ重要なのか
品質管理(英語:Quality Control/略してQC)とは、製品を製造する工程において、その品質の向上を目指し、品質を管理する取り組みのことです。具体的には、品質の一貫性を確保するために検査、検証し、保証することを指します。完成品はもちろん、完成までの生産工程についても管理します。
製造業において重要なQuality(品質)・Cost(コスト)・Delivery(納期)を最適化し(QCDの最適化)、顧客の満足を得るためには、欠かせない管理です。
質管理を行うことによって、製造業の現場から市場に向けて、不良品を出さず、品質の安定した製品を効率的にコストをかけず提供することが可能になります。
品質管理と「品質保証」の違い
品質管理と似た概念として、品質保証(英語:Quality Assurance/略してQA)があります。品質管理と品質保証は、管理する対象と範囲が異なります。
業務名 | 品質管理 | 品質保証 |
管理する対象 | 生産から販売まで一連の流れ | 製品の品質の保証 |
管理する範囲 | 出荷前までの品質 | 流通した後の品質まで。消費者への責任を負う |
品質管理は、製品の品質の保証に焦点を当てた品質保証の一部です。
品質管理に関する規格「ISO9001」
品質管理に関連する規格としては、品質マネジメントシステム(QMS)の国際規格であるISO9001があります。
ISO9001は、一貫した製品・サービスの提供と顧客満足の向上を目指し、組織の品質活動や環境活動を管理するための仕組み(マネジメントシステム)について制定されているISO規格です。
企業がISO9001を取得するメリットは、「製品に対し、顧客の信頼性が向上すること」だと言えます。なぜなら、ISOは取得後も毎年審査が行われるため、それをクリアし続けるためには、継続的に品質改善を行う必要があるためです。結果として、常によりよい製品を世に送り出すことができ、顧客の信頼性アップにつながることが期待できます。
※ISOとは
ISOはInternational Organization for Standardization(国際標準化機構)の略称で、スイスのジュネーブに本部を置く非政府機関のことです。ISOは、国際的な取り引きをスムーズにするために、さまざまな製品やサービスに関して国際的に通用する基準を設け、ISO規格を制定しています。全世界で170カ国以上、100万以上の組織が利用しています。
(参考:一般財団法人日本品質保証機構「ISO 9001(品質)」)
品質管理に関する資格「品質管理検定(QC検定)」
品質管理や品質保証に携わる人を対象にした資格として、日本規格協会グループが実施する「品質管理検定(QC検定)」があります。品質管理に関する知識をどの程度持っているか、客観的に評価する検定です。
4段階の級が設けられており、最もレベルの高い1級/準1級は、企業内で品質管理全般の知識が要求される業務に携わる人が対象です。
個々の品質管理の知識レベルに合わせた勉強や受験をすることで、品質管理に関するスキルを段階的に向上させることができます。
(参考:日本規格協会「品質管理検定(QC検定)とは」)
品質管理に必要な3つの要素
品質管理業務は、主に「工程管理」「品質検査」「品質改善」の3要素から構成されます。それぞれくわしくみていきましょう。
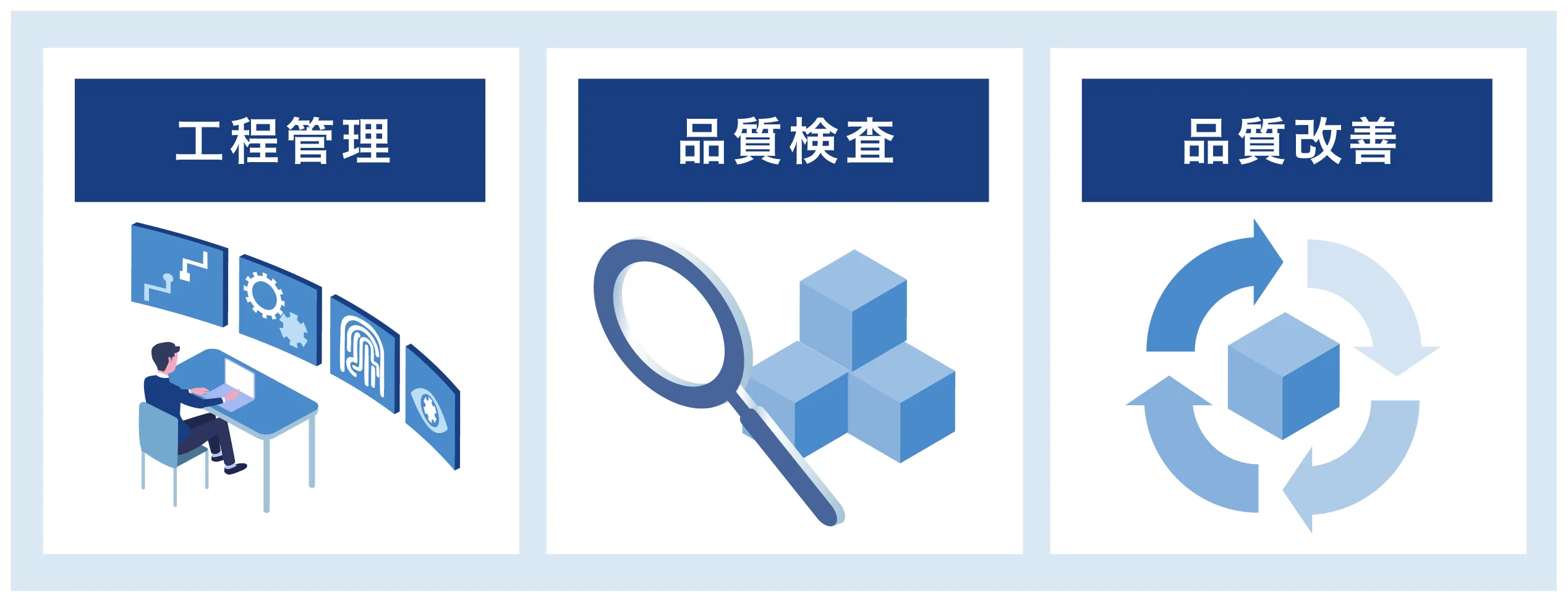
工程管理
工程管理とは、作業員・資材や原料・機械や設備・作業方法など製造工程に関わる製品づくりの進捗や実績などを管理する業務のことです。製品の品質を保ち、必要数量や納期を守ったうえで、生産性を向上させることを目的としており、製品やサービスの品質を総合的に管理する品質管理の一環として行われます。工程管理表を使いながら、管理していきます。
【関連記事】工程管理とは?システム・ツール活用術や課題解決のポイントを解説
品質検査
品質検査は、要求仕様や品質基準に適合しているかを確認する業務のことです。検査するものは完成品だけに留まりません。部品・資材の受け入れ時の「受け入れ検査」、各製造工程の「工程内検査」、倉庫に保管していた製品出荷時の「出荷検査」など、各工程において必要な検査を行います。画像認識を駆使した最先端のシステムなどを使い、作業員の工数を減らし、高度な検査を行うパターンもあります。
品質検査においては、そもそもの検査項目や合格ラインの設定自体に問題がないかという点も重要になります。
品質改善
品質改善は、品質を向上させるための取り組みを行う業務のことです。不良品の発生予防および再発防止を目指します。
品質改善の手法としては、不良品の再発を防ぐための「QCストーリー(データ収集して現状を把握し、不良品発生の原因を分析した上で対策を講じ、解決を図る)」や、不良品を未然に防ぐ「工程FMEA(製造プロセスで懸念される要因を洗い出し、不良品発生の予防を図る)」などが用いられます。
品質管理に使われる9つの手法・ツール
品質管理を進めるにあたって使われる手法をご紹介しましょう。
<手法1>QC7つ道具
QC7つ道具(Quality Control Seven Tools)は、数値データを集計し、品質管理を定量的に分析し改善・解決するために用いられる手法です。
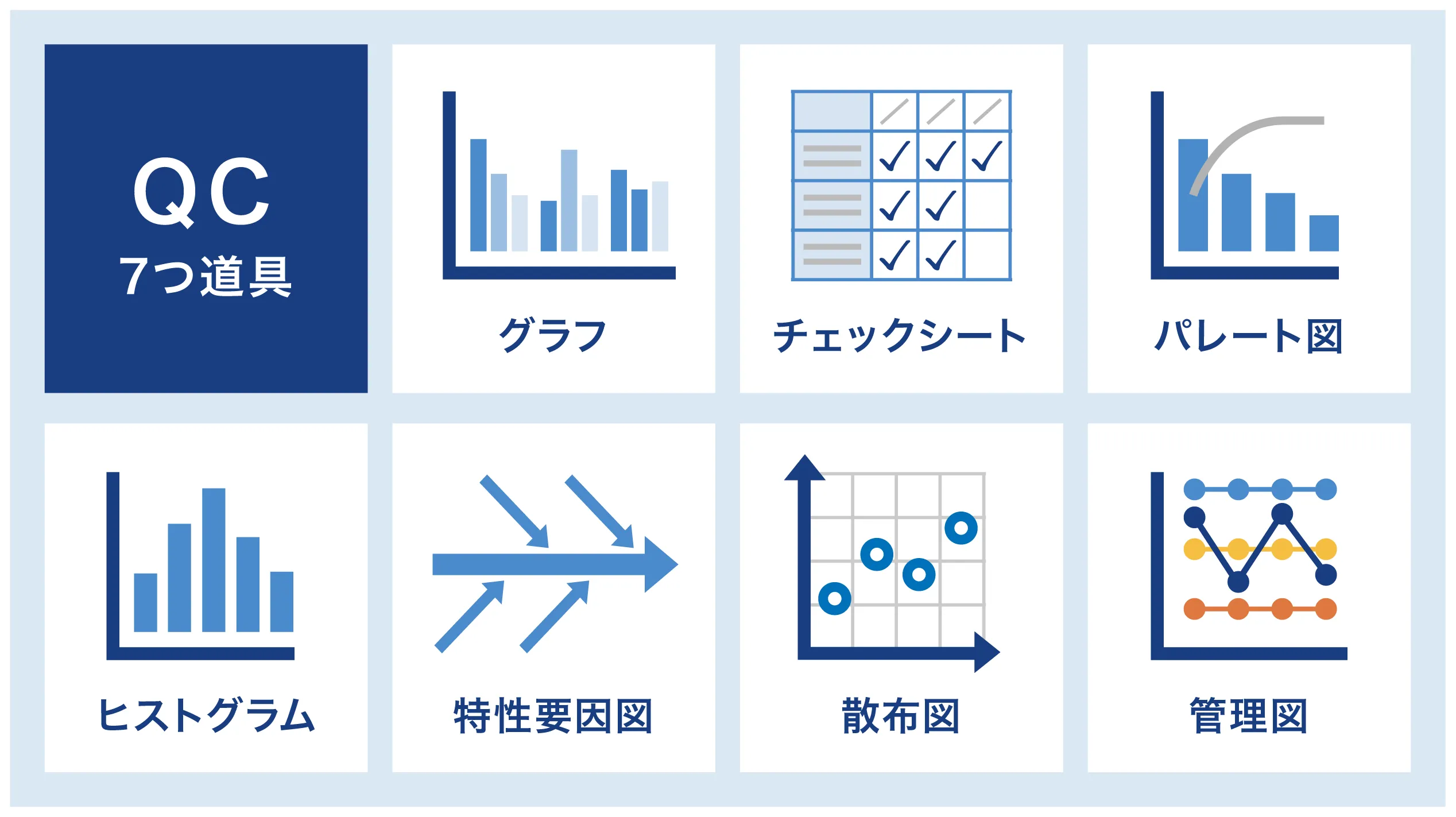
具体的な7つの道具についてみていきましょう。
グラフ
数値データで、傾向や変化、大小関係などの比較を可視化でき、全体の情報を俯瞰できます。棒グラフ、折れ線グラフ、帯グラフ、円グラフ、レーダーチャートなどがあります。
チェックシート
指定項目の結果を記録する図表形式のシートです。チェックの合否や点検結果など、測定結果を正確に記すことで、改善のためのデータを収集できます。
パレート図
棒グラフ(データ項目を降順に並べる)と線グラフ(各項目の累積比率を示す)を複合的に用いて、優先的に改善すべき点を可視化できます。
ヒストグラム
任意の区分ごとに、データの分布状況を可視化できる棒グラフです。平均値や異常値、ばらつきを確認でき、問題が生じる原因を追求できます。
特性要因図
問題となっている特性(結果)が、どのような要因で構成されているかを分類する図です。因果関係を可視化し、理解するために用いられます。魚の骨のような形に見えることから、別名「魚の骨図(fishbone diagram、fishbone chart)」とも呼ばれます。
散布図
関連する2種のデータを縦軸と横軸に置き、点の集合で結果を示した図です。2種のデータの相関性を視覚的に把握できます。
管理図
時系列で工程ごとのデータを表示した折れ線グラフです。どのような仕組みで品質のばらつきがあるか判定・分析し、その原因が対策可能なのか(異常原因)、対策が難しいのか(偶然原因)を判断できます。
<手法2>新QC7つ道具
製造業の工程において、全てが数値として表れるとは限らず、データとして扱えない場合、QC7つ道具は使えません。そこで登場するのが、新QC7つ道具(New Quality Control Seven Tools、略称:N7)です。数値化できないデータを集計し、品質管理を定性的に分析し改善・解決するために用いられる手法です。
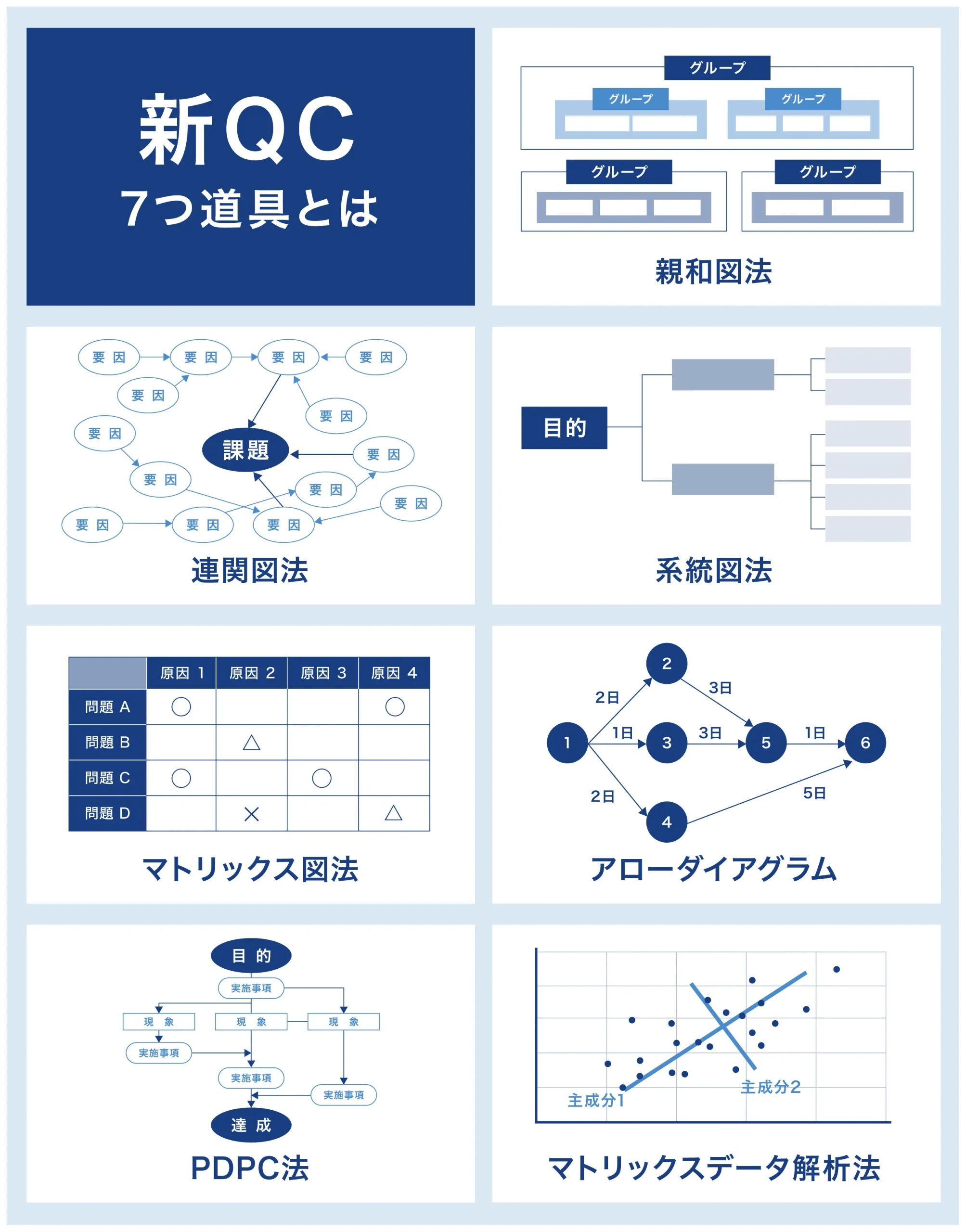
具体的な7つの道具について、みていきましょう。
親和図法
ある問題から収集された、まとまりのない言語データを親和性(関連性)の高いグループに分け、整理・体系化する方法です。課題を明確化できます。
連関図法
複雑に絡み合った問題の原因と結果、目的と手段などについて、それぞれの因果関係を論理的につないでいく方法です。因果関係を見つけた上で主要因を追求できます。
系統図法
目的達成のために最適な手段や方法を、枝分かれさせながら多段展開していく方法です。この展開により、現実的に実行できそうな最終的な手段にたどり着くことができます。
マトリックス図法
検討するふたつの要素を「列」と「行」に分け、2つの交点に関連の有無や度合いを表示し、その対応関係を明らかにする手法です。各要素間の関係整理、全体を見渡すことで問題解決への糸口がわかります。
アローダイアグラム
問題解決のための作業順序を矢印や結合点で結んでいくことで作図します。全体を把握し、最適な日程計画をする時に用いられます。
PDPC法
想定されるさまざまなリスクを洗い出し、目標達成までに不測の事態が起こっても代替できる案を明確にしておく方法です。プロセス設計図とも言います。
マトリックスデータ解析法
例外的に数値データを扱います。マトリックス図の「行」「列」に配置された数値データを解析し、二次元平面図に表示する手法です。データの特徴や新たな指標や情報を引き出せます。
<手法3>PDCAサイクル
PDCAサイクルとは、Plan(計画)、Do(実行)、Check(評価)、Action(改善)の頭文字を取った業務改善のためのフレームワークです。「計画・実行・評価・改善」が1周したら終わりではなく、4つのプロセスを繰り返すことによって、品質管理の持続的な改善が期待できます。
PDCAサイクルがうまく回らない時は、4つのプロセスのどこかに必ず原因があります。回すことが基本となる手法なので、うまく回せるよう心がけましょう。
<手法4>IE
IE(Industrial Engineering、日本語訳:生産工学、産業工学)とは、科学的・論理的な分析によって、生産性を向上させる手法を指します。製品を適切な品質と価格で製造・販売するために、予算・原価管理、作業手順、人員配置など「経営上必要な工程」を工学的手法のもと進めていきます。
<手法5>5S
5Sとは、製造現場環境を適切に管理、維持していくために必要な5つの考えや活動を指します。以下の5つの言葉の頭文字をとっています。
- 整理/Seiri
- 整頓/Seiton
- 清掃/Seisou
- 清潔/Seiketu
- 躾/Situke
設備投資などの多大な費用をかけることなく、誰でも簡単に取り組めるのが5Sの利点です。人為的ミスを減らし、企業の経営体質の改善も望めます。
<手法6>4M
4Mとは、製品の品質を管理するために必要な4つの要素を指します。以下の4つ言葉の頭文字をとっています。
- 人/Man
- 機会・設備/Machine
- 方法/Method
- 材料/Material
適切に4Mを管理すれば、品質管理はもちろん、課題の発見と解決、顧客満足度の向上、製造コストの削減、生産の効率化なども実現できるでしょう。
<手法7>TQC
TQC(Total Quality Control、日本語訳:全社的品質管理)とは、文字通り全社的な品質管理のこと。つまり、品質管理に関するさまざまな手法を総合的に、かつ、全社的に展開して適用し、従業員の総力を結集してその企業の実力向上を目指します。
品質管理の担当者だけでなく、従業員一人ひとりが主体的に取り組むことが求められます。
(参考:日本産業標準調査会ウェブサイト)
<手法8>TQM
TQM(Total Quality Management、日本語訳:総合的品質管理)とは、経営全体での品質向上管理を目指すことを指します。具体的には、品質を中核におき、顧客や社会のニーズを満たす製品・サービスの提供と、労働者の満足を通じた組織の長期的な成功を目的としています。
活動としては、全部門・全階層が参加して、プロセス及びシステムの維持向上、改善及び革新をさまざまな手法を駆使し、経営環境の変化に適した効果的・効率的な組織運営を実現していきます。
TQMはTQCを発展させたものでありTQCと似ている手法ですが、TQCでは品質管理を担う主体は現場の従業員です。一方TQMでは、経営陣からのトップダウンの形で品質管理が行われます。
(参考:社団法人 日本品質管理学会「品質管理用語」)
<手法9>SQC
SQC(Statistical Quality Control、日本語訳:統計的品質管理)とは、統計的方法を用いて品質管理を行い、品質の安定や向上を図ることを指します。
製造業では多くの場合、同製品を大量に製造するため、製造した全製品の品質を測定するのは困難です。そのため、少数を抜き出しサンプルとして品質測定をします。その際、QC7つ道具の管理図や相関分析、回帰分析、実験計画法、多変量解析法など統計的な手法を使って解析を行い、品質のバラツキが偶発的なものか原因があるものなのか見極め、基準や標準を決定していきます。
品質管理における課題
製造業の品質管理においては、主に以下の課題が挙げられます。
- データが多く管理が追いつかない
- 部門間の連携不足
- 持続的な改善の困難さ
- 実施した施策が現場に定着しない など
それぞれどのようなことか、みていきましょう。
データが多く管理が追いつかない
製造する製品が多数だったり、品質管理をする対象が広範囲だったりと、解析するためのデータは膨大です。高い品質を維持するためには、さまざまな手法を用いる必要もあり、手法が増えればその分、収集できるデータも多くなります。その結果、管理が追いつかないという問題が生じてしまいます。
部門間の連携不足
製造業においては、工程が多岐にわたるため、製造部内でも工程ごとチームなどに分かれる場合が多いです。また、製造部や品質管理部以外にも、資材部、営業部、開発部など関わる部門が多いのも特徴です。
それぞれの部門で管理しているデータも多いので、部門間の連携が不十分だと、数量や仕様にミスが生まれるといった問題につながることがあります。
持続的な改善の困難さ
品質管理を進める中、ある工程において問題が発見されたとします。それを改善しても、それで全てが終わるわけではありません。検査、発見、改善を持続していかなければ製品の品質向上にはつながりません。
品質管理では、PDCAサイクルのように方法を継続していくことで新たな課題をキャッチし、それを改善につなげていくことが大切です。しかし、人員やコミュニケーションなどの不足により難しいことがあります。
実施した施策が現場に定着しない
これまでに紹介した手法も用いて改善策を打ち出したとしても、それを実施し定着しなければ、品質管理がしっかりと出来ているとは言えません。実施したい施策が現場で本当に遂行できることなのか、人的配置や工数、内容、期間など複合的な視点で検証することが大切です。
適切な品質管理を目指すなら「生産管理システム」もおすすめ!
上記で述べた品質管理の課題を解決する方法の一つとして、「生産管理システム」を導入することが挙げられます。生産管理システムとは、受注管理や生産計画、購買管理や在庫管理など、生産管理におけるさまざまな業務を管理するシステムのことを指します。
生産システムの活用により、品質管理業務も効率化することができます。ここでは、おすすめの生産管理システムとして、キッセイコムテックが開発・販売している「ProAxis(プロアクシス)」をご紹介します。
ProAxisについて
「ProAxis」は、現場ニーズを重視し、「適応性」「操作性」「柔軟性」を考慮した生産管理システムです。キッセイコムテックが、30年にわたる製薬メーカーの情報子会社としての経験と、数多くの製造業へのシステム導入により培った業務ノウハウを基に開発しました。
ProAxisの特徴
「ProAxis」は、工場の基幹業務を全てカバーできる統合型のシステムです。そのため、品質管理機能もご用意しています。品質管理においての特徴は以下をご覧ください。
各検査項目を定義、判定に用いる閾値をマスタに登録可能任意のロットに対し検査実績を登録可能検査実績ピックアップによる合否判定のシステム化製品仕様データの共有によるミスの軽減BIツールによる品質管理の可視化導入していただく企業さまに合わせてカスタマイズし、最適な品質管理をサポートします。
ProAxisの品質管理オプション機能
基本システムをより一層効果的に運用できるよう、オプション機能として「eXsiteDesigner」をご用意しております。
eXsiteDesignerを追加すれば、手書きのチェックシートを簡単にデータ化したり、ExcelシートをWebアプリに自動変換したりすることができ、簡易なWebシステムとしてご利用いただけます。これまでExcelを使っていた方にも、使い慣れた操作方法で運用できると好評です。
ProAxisを導入するメリット
「ProAxis」の導入にあたっては、“安心のOne Stop Service”として、要件定義から本稼働まできちんとサポートいたします。また、本稼働後もお客さまごとに専用の保守問合せ窓口「i-Support」をご用意し、万全なサポート体制でバックアップします。
更なる事業規模拡大、新たな事業展開に向けたIT基盤づくりを全面的にご支援します。システム関連でのお悩みや問題は、全てお任せください。
「量産」にも「個別受注」にも対応できる生産管理・債権債務管理システム「ProAxis」
品質管理の重要性や手法を知り、あるべき姿をイメージしよう
品質管理は、高い品質を維持し、コスト的にも適正で、顧客の満足と信頼を得るためには製造業の要と言っても過言ではありません。正しい品質管理活動を遂行するためには、さまざまな手法の中から最善な方法を使っていく必要があります。しかし、管理する範囲が多岐にわたるため難しいのが現状です。生産管理システムや品質管理システムも上手に活用しながら、満足のできる品質管理を行っていきましょう。